Sugar Coating of Tablets
Sugarcoating of tablets is not as common in the pharmaceutical industry. Since it has been replaced by Polymer film coating. The sugar coating is generally water-soluble making it easier to dissolve quickly when it comes into contact with any liquid medium such as gastrointestinal fluids. One purpose of the sugar coating is to protect the drug inside the tablet and act as barrier to external contaminants. It may also hide or mask the unsavoury taste of the drug that some patients may find unpalatable. Sugarcoating insulates and masks the colour and texture of the tablet’s core.
Advantage of Sugar Coating
- The process requires low capital cost, unsophisticated equipment and is relatively easy to perform i.e. inexpensive and readily available raw materials.
- It is affordable in terms of running costs as the most common ingredients used are sugar and water.
- It provides an attractive and glossy finish.
- Sugar coated tablets are easy to swallow as the sugar masks the taste.
- Sugar coating process is generally not as critical (as film coating)
Disadvantages of Sugar Coating
- It requires specialized and trained personnel
- The process is Labour intensive
- It requires long processing time
- Sugar coated tablets are not amenable to embossing, use of print for identification or labelling
- Sugar coating increases the weight and size of the tablet
Raw Materials for Sugar Coating
Sugar & it’s Substituents: Glucose, lactose, isomalt, sugar alcohols
Binders: Acacia, gelatin, PVP
Colouring agents: Water-soluble (dyes), water-insoluble (lakes)
Anti-Adherents: Talcum, colloidal silica
Fillers: CaCO3, CaSO4, starch, talcum, TiO2
Polishing Agents: beeswax, carnauba wax, paraffin
Other agents: Flavouring agents, surfactants
Sugar Coating Process of Tablet
The coating process involves the repetitive application of a sucrose-based solution to cover the tablet n the coating pan or drum.

Process steps are commonly employed, in the following order:
- Sealing of the tablet core/ (Water proofing) – sealing involves hardening the external surface of the tablet by providing a moisture barrier.
- Subcoating
- Smoothing
- Colour coating- provides the tablet the appropriate colour for the end product.
- Polishing-finishes the tablet by polishing to give the tablet a glossy and professional appearance.
- Printing
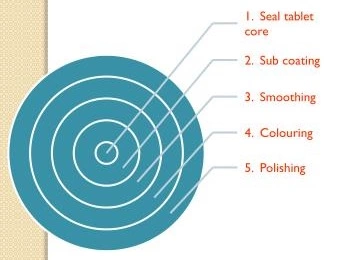
i. Sealing (Water Proofing)
The core of the tablet is usually weak and has high propensity for disintegration. The core would therefore likely be the first to disintegrate during the coating process. So that, It is usually required to prevent the tablet core and its contents from absorbing water, softening, and initiating disintegration during the subsequent steps of the sugar-coating process.
Sealants that are commonly used include:
- shellac,
- zinc oxide,
- cellulose acetate phthalate,
- polyvinylacetate phthalate,
- hyroxylpropylcellulose,
- hyroxypropylmethylcellulose
ii. Subcoating
- Subcoating is applied to tablet core to make the sides of the tablet rounded or shaped up to the desired appearance.
- to round off sharp edge of core (smooth surface is not required)
- to provide a good substrate for subsequent smoothing step
- There are two methods of Subcoating:
- A gum based solution or syrup is coated on the tablet. The tablet is then dried. The procedure is repeated until the desired tablet shape is achieved.
- Dry powder is applied followed by gum/sucrose solution. Once applied, the gum/ solution excess water is removed by drying so as to harden the surface again.
- Subcoating usually involves alternating gum solution with dusting powder (talc or calcium carbonate) until the desired shape and consistency is achieved. Excess water is removed after every syrup application.
iii. Grossing (Smoothing)
The Grossing or smoothing step involves filling out and smoothing irregular features or areas of the tablet. The process gradually also increases the size of the tablet to the required dimensions.
- to smooth the rough core surface.
- to provide a smooth base for color coat
iv. Colouring
Colouring coating is the most crucial penultimate stage in the coating process as multiple sugar solution is added to ensure that the predetermined colour is achieved.
It involves the multiple application of syrup solutions (60–70% sugar solids) containing the requisite coloring materials necessary to achieve the desired shade.
Sugar-coating colorants may be subdivided into either water-soluble dyes or water-insoluble pigments.
Traditionally, water-soluble dyes have been used because they produce the most elegant sugar-coated tablets but in order to speed up the coating process, minimize color migration problems, and ensure color reproducibility from batch-to-batch, water-soluble dyes have gradually been replaced with water-insoluble pigments in pharmaceutical tablet coating. Tablet color coating with water-insoluble pigments have demonstrable advantages over water-soluble dyes, two important ones being:
- Lack of solubility in aqueous media which eliminates color migration during drying
- Superior light stability
v. Polishing and/or printing
- The final step in the sugar coating process is a polishing step. This is carried out to impart a shiny distinctive appearance to the tablet. An application of wax such as carnuba wax, candelila wax, beeswax and hard paraffin is used to polish the tablets inside a polishing pan.
- Finally, tablet markings or brands may be printed on the surface of the tablet using edible ink.
Defect of Sugar coating tablet
Common Problems that can occur during the sugar coating process and their solutions are below
- Chipping of the tablet coating
- Cracking
- Non-drying of the coating
- Twinning
- Uneven colouring
- Blooming and Sweating
- Marbling
Read more here about the defect of Sugar-coating tablet
Comments are closed