During the process of size reduction, it is not possible to obtain the particle of uniform size. Hence special technique is used to separate particles of a specified size, which is known as the process of size separation. Size separation is also known as sieving, sifting, screening. This technique is based on physical differences b/w the particles such as size, shape and density
Official Standard for Powder: IP (Indian Pharmacopoeia)
Coarse or fineness of powder is expressed by Reference to the nominal mesh aperture size of the sieve through which powder is able to pass.
- Indian pharmacopoeia- 5 grade of powder
S. No. | Grade of powder | all particles must pass through Sieve No. /Nominal mesh aperture | Sieve through which 40% of the particles pass/ Nominal mesh aperture | Comparison of powder size |
---|---|---|---|---|
1 | Coarse powder | 10 /(1.70 mm) | 44 /(355 µm) | 1 |
2 | Moderately coarse powder | 22 /(710 µm) | 60/ (250 µm) | 1/6 |
3 | Moderately fine powder | 44/(355 µm) | 85/(180 µm) | 1/24 |
4 | Find powder | 85/(180 µm) | Not specified | 1/90 |
5 | Very fine powder | 120/(125 µm) | Not specified | 1/2000 |

A) Coarse Powder:
- A powder, all the particles of which pass through a sieve with nominal mesh aperture of 1.70 mm (Sieve No. 10 ) and not more than 40% pass through nominal mesh aperture of 355 µm (Sieve No. 44) is called a Coarse Powder.
B) Moderately Coarse Powder:
- A powder, all the particles of which pass through a sieve with nominal mesh aperture of 710 µm (Sieve No. 22) and not more than 40% pass through nominal mesh aperture of 250 µm (Sieve No. 60) is called a Moderately Coarse Powder.
C) Moderately Fine Powder:
- A powder, all the particles of which pass through a sieve with nominal mesh aperture of 355 µm (Sieve No. 44) and not more than 40% pass through nominal mesh aperture of 180 µm (Sieve No. 85) is called a Moderately Fine Powder.
D) Fine Powder:
- A powder, all the particles of which pass through a sieve with nominal mesh aperture of 180 µm (Sieve No. 85) is called a Fine Powder.
E) Very Fine Powder:
- A powder, all the particles of which pass through a sieve with nominal mesh aperture of 125 µm (Sieve No. 120) is called a Fine Powder.
- Note:
- For Fine & Very fine grade of powder: IP has prescribed only the upper limit (Fine & Very fine)
- Fineness of powder is described by means of Number: it indicates that all particles of powder shall pass through that sieve number (respective nominal mesh aperture in µm).
Sieves number (square meshes)
In the pharmaceutical industry, sieves and screens are regularly used to determine the size of raw materials. The most common way to measure the sieves and screens is with meshes. On average, about 40 to 400 sieves are used in the industry, especially during the milling and sifting of raw materials.
Number of meshes
Number of meshes included in a length of 2.54 cm (25.4 mm) in each direction parallel to the wire.
A mesh shows the available opening in one linear inch of a screen or sieve; a 10-mesh sieve has 10 openings, whilst, a 300-mesh sieve will have 300 available openings in a linear inch. The fineness of the screen or sieve will depend on the wire width. A wire that is used for a 10-mesh sieve is thicker than one that is used for a 60-mesh sieve;, a thin wire will not work for a thick sieve and a thick wire won’t be used to make a fine sieve.
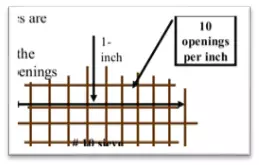
Determining the Mesh Size of Different Screen Size
To obtain the mesh size of any screen type, follow these simple steps:
- Mark the sieve about 1 inch using a marker and a scale
- To be more accurate, start measuring from the center of the wire
- Start counting the holes in one linear inch
Example: if there were 40 holes in one linear inch, it would be 40-mesh in the sieve.
- Nominal size of the aperture (hole):
- Distance between the wires
- Square aperture-length of the side of square aperture
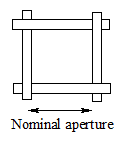
- Nominal diameter of the wire:
- wire diameter (wire should be uniform circular cross-section and should not be coated plated)
- Approximate percentage saving area: area of meshes as a percentage of the total area of the sieves.
- Generally sieving area range- 30-40 %

- Tolerance average aperture size: Some variation in the aperture size is unavoidable and when this variation is expressed as a percentage, it is known as the ” aperture tolerance average”
- Perforated plate sieve: made by drilling hole in metal plate- circular apertures
- Have greater accuracy than wiremesh sieve
- Used in screen of impact mills
The material used for sieves:
- Wire: should be uniform, circular cross section, no distortion, resistance to corrosion by any substance.
- Metals
- Iron and coated iron
- Copper and copper alloy
- Stainless steel(most satisfactory and good resistance to corrosion)
- Non metal (used when metallic contamination is contraindicated)
- Nylon & terylene
- Metals
PERFORATED PLATE SIEVES
Sieves may also be made by drilling holes in metal plate, so that this type will have circular apertures as against the square apertures of the wire mesh sieve.
Greater accuracy than wire-mesh sieves, as well as being less susceptible to distortion in use. This type is commonly used also as screens in impact mills.
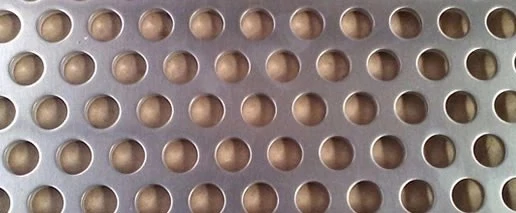
Principles of Mechanical Size Separation
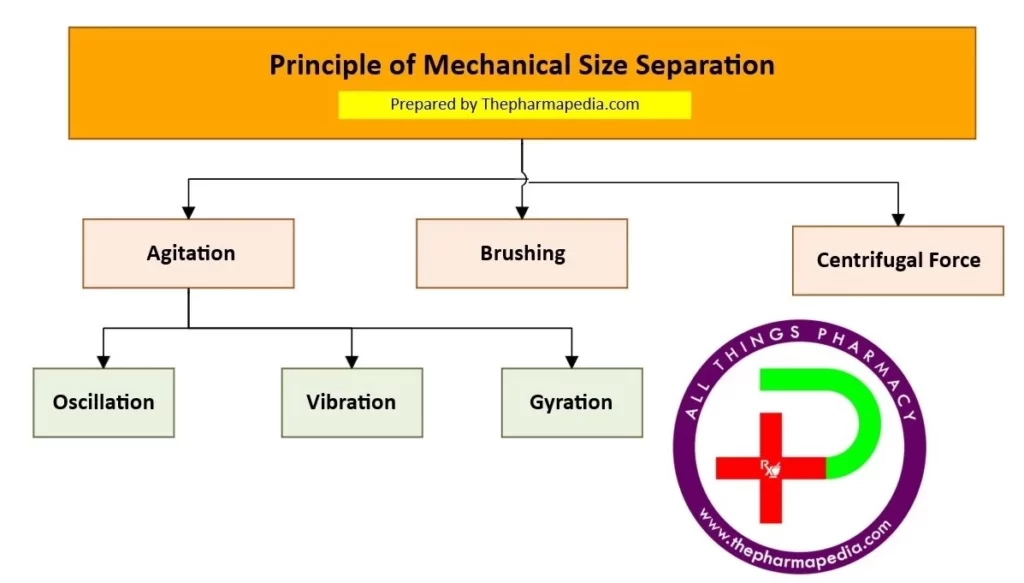
a. Agitation:
- Sieves may be agitated in a number of different ways.
- Oscillation (move back and forth)
- The sieve is mounted in a frame that oscillates.
- Advantages: Simple method
- Disadvantages: The material may roll on the surface of the sieve and fibrous materials tend to “ball”.
- Vibration:
- The mesh is vibrated at high speed, often by an electrical device.
- Advantages The rapid vibration is imparted to the particles on the sieve and the particles are less likely to “blind” the mesh.
- Gyration:
- Sieve is rubber mounted and is connected to an eccentric flywheel which gives gyrating movement which helps particles passing the sieve.
b. Brushing:
- A brush can be used to move the particles on the surface of the sieve and to keep the meshes clear.
- A single brush across the diameter of an ordinary circular sieve, rotating about the midpoint, is effective;
- In large-scale production a horizontal cylindrical sieve is employed, with a spiral brush rotating on the longitudinal axis of the sieve.
- Useful for separating sticky powder particles.
c. Centrifugal Force:
- Use a vertical cylindrical sieve with a high speed rotor inside the cylinder, so that particles are thrown outwards by centrifugal force.
- The current of air created by the movement helps sieving.
- Is especially useful with very fine powders.
Method of Size Separation

1. Sieving method of size separation/Sieve Shaker
Sieve arrangement:
- Descending order or sieve of large size is at the top and smallest is at the bottom.
- Materials displaced in the uppermost sieve.
- Mechanism of action of sieving involved:
- Agitation (oscillation, vibration, gyration)
- brushing
- Centrifugal
Advantage of sieving method: Rapid process with the requirement of little skill

2. Cyclone separator
Principle: centrifugal force is used to separate solid from fluidised in air. (Separation depends on particle size & Density).
Solids are suspended in air and Force air introduced tangentially at Higher velocity so that Rotary movement take place.
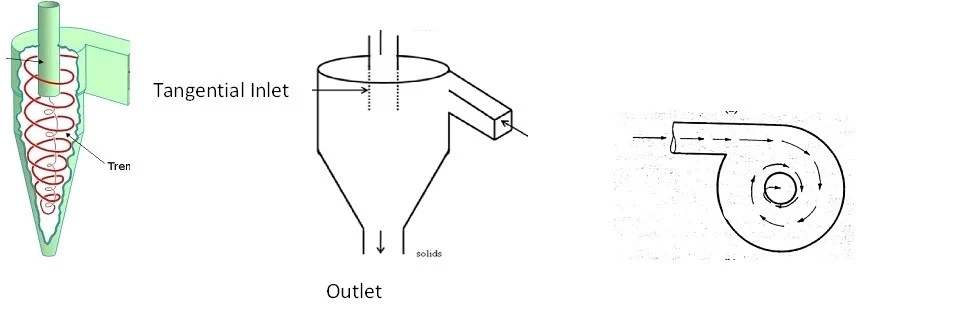
3. Air separator
Air movement is obtained by rotating disc/blood in vessel (Principle: centrifugation)

Uses: air separator is option connected to ball mill or hammer mill to separate and return oversize particle for further size reduction.
4. Elutriation method:
Elutriation depends on the movement of a fluid against the direction of sedimentation of the particles And it is a continuous process. (Separation of fine particles & coarse particles form a paste/levigation.
Multi stage Elutriator

Use: separation of course and fine particle of powder after levigation (suspension)
it is continuous separation process but need to dilute suspension (2%) of solid particle which is not desirable.
5. Sedimentation tank
A suspension of the solid in a liquid is placed in a tank and allowed to stand for a suitable time.
Continuous sedimentation tank: A shallow tank is arranged with inlet and outlet pipe.
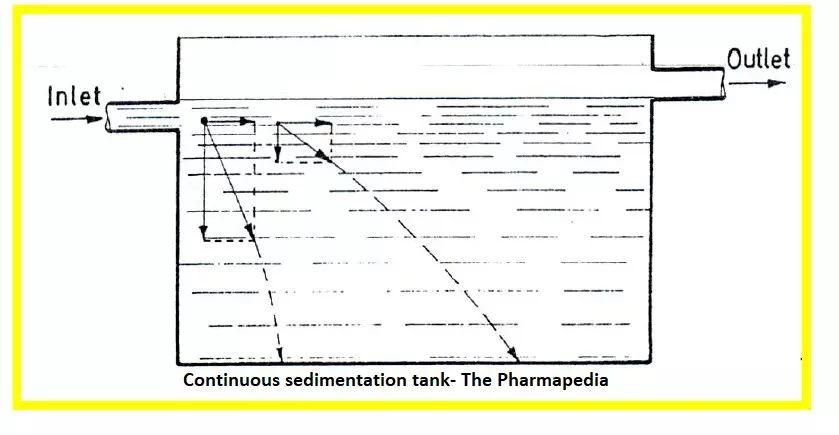
Comments are closed